Hydrogen cylinders, the safe choice for hydrogen storage. In order to meet the demand of hydrogen energy wide application, high pressure hydrogen storage becomes the preferred technology. Our hydrogen cylinders are based on high pressure hydrogen storage and use advanced design and manufacturing processes to support the development of hydrogen energy. The nominal working pressure is carefully designed in the range of 35-70MPa. Hydrogen cylinders are divided into four types, each of which is rigorously tested and validated. All-metal gas cylinder (type I) and metal inner liner fiber ring winding gas cylinder (type II) not only have the characteristics of high pressure hydrogen storage, but also ensure the advantages of simple structure, fast filling and discharge speed. The metal and non-metal cylinders (type III) and the non-metal cylinders (type IV) with full fiber winding structure not only have low weight to volume ratio, but also have high hydrogen storage density per unit mass. This makes them ideal for hydrogen storage in hydrogen fuel cell vehicles. Our hydrogen cylinders have not only undergone rigorous quality tests, but have also passed a number of safety performance tests. We are committed to providing users with safe and reliable hydrogen storage solutions to ensure the wide application of hydrogen energy
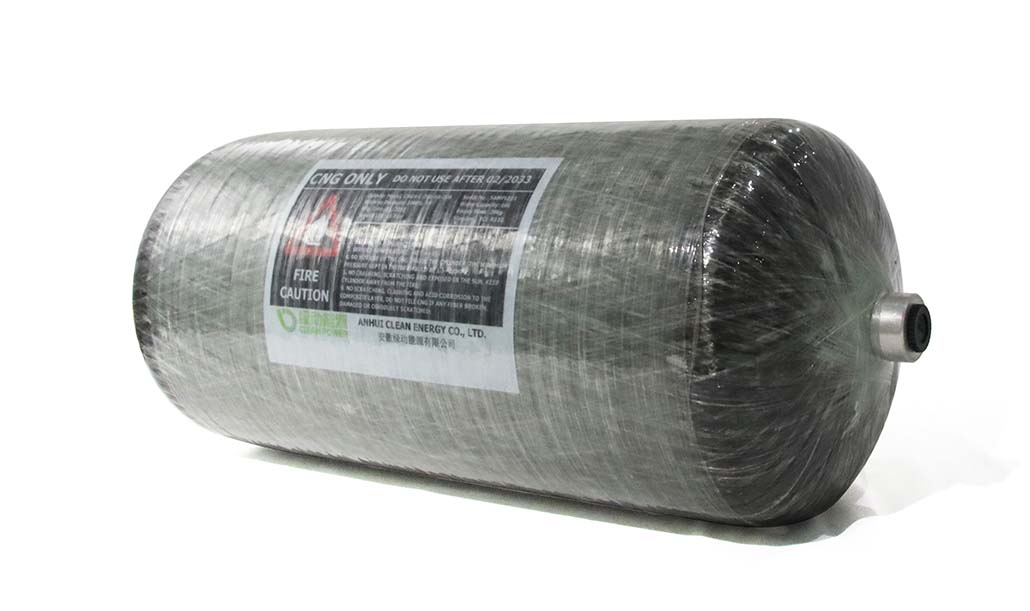
Compare different types of hydrogen cylinders
With the rapid development and industrialization of hydrogen fuel cells and electric vehicles, the problem of hydrogen storage and transportation is becoming a research hotspot all over the world. Hydrogen storage bottle is a very important storage and transportation medium, the following table lists the performance comparison of different hydrogen storage bottles
Types |
type I |
type II |
type III |
type IV |
type V |
material |
Pure steel metal bottle |
Metal liner (steel) fiber loop winding |
Metal liner (steel/aluminum) fiber fully wound |
Plastic liner fiber fully wound |
No liner fiber fully wound |
Working pressure (Mpa) |
17.5-20 |
26-30 |
30-70 |
30-70 |
Research and development at home and abroad |
Dielectric compatibility |
Hydrogen brittle and corrosive |
Hydrogen brittle and corrosive |
Hydrogen brittle and corrosive |
Hydrogen brittle and corrosive |
Weight volume (kg/L) |
0.9-1.3 |
0.6-1.0 |
0.35-1.0 |
0.3-0.8 |
Service life (years) |
15 |
15 |
20 |
20 |
cost |
low |
intermediate |
Highest |
high |
Onboard or not |
no |
mo |
yes |
yes |
Market application |
Hydrogen station and other fixed hydrogen storage |
Fuel cell vehicle |
IV hydrogen storage cylinder structure and materials
The composite hydrogen storage cylinder consists of lining material, transition layer, fiber winding layer, outer protective layer and buffer layer from inside to outside. The cycle required for filling the hydrogen storage tank may be relatively long, and the hydrogen gas has strong permeability under high pressure, so the lining material of the hydrogen storage tank must have a good barrier effect, so as to ensure that most of the gas can be stored in the container. IV hydrogen storage cylinder structure includes an inner liner, an intermediate layer and a surface layer
The resin matrix of carbon fiber hydrogen storage cylinder needs to meet the requirements of mechanical strength and toughness. Because it is easy to fatigue damage after long-term aeration and degassing, a high-strength and fatigue-resistant resin system is needed to ensure the life of the cylinder. In addition to the performance of the wet winding resin matrix, it also requires low initial viscosity and long service life at operating temperature. Epoxy resin has many advantages, wide sources and reasonable price, and is suitable for wet winding process. It is one of the thermosetting resin substrates commonly used in composite material layer of type IV high-pressure hydrogen storage cylinder.
The fiber winding molding process of type IV hydrogen storage bottle can be divided into wet winding and dry winding. The carbon fiber winding molding process adopted by Anhui Clean Energy Co., Ltd. is wet winding. The wet winding equipment mainly includes fiber frame, tension control equipment, dipping tank, spinning nozzle and rotating core mold structure. We use a combination of spiral winding and circumferential winding, the circumferential winding can eliminate the circumferential stress caused by the internal pressure of the cylinder, and the circumferential winding can provide longitudinal stress to improve the overall performance of the cylinder.
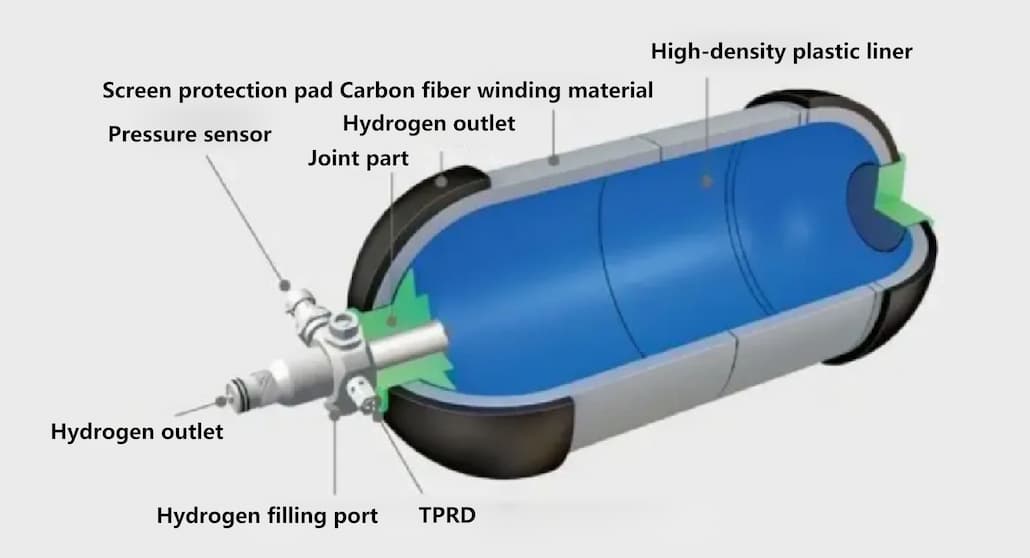
The wet winding process is to impregnate the carbon fiber strands in a specific dipping device, then wrap them directly on the mandrel under tension control, and finally cure the forming method.
Its main advantages are as follows:
(1) The product has good air tightness, and during the winding process, the excess resin glue can be extruded from the bubble through tension control, and the gap can be filled.
(2) The resin adhesive impregnated on the surface of carbon fiber can effectively reduce fiber wear.
(3) Good parallelism of fiber arrangement.